In today’s competitive market, creating customer-centric products is more important than ever. Quality function deployment (QFD) is a methodology designed to help organizations achieve this by prioritizing the voice of the customer (VOC) throughout the product development process.
By using a structured approach, QFD ensures that customer needs and preferences are taken into account, resulting in products that are more likely to satisfy your target audience.
In this guide, we’ll explore the key components of QFD, including the house of quality and the VOC. We’ll also delve into the four phases of the QFD process and provide a practical example of how it can be applied in product development.
Read on to learn how QFD can help your organization create products that truly resonate with your customers.
Table of contents
What is quality function deployment (QFD)?
Quality function deployment (QFD) is a methodology for gathering customer requirements and turning them into products or services. It emphasizes listening to the customers’ needs and wants before deciding what product features or services to create to meet those demands.
The QFD methodology is meant to supplement an organization’s current design process. It’s a method to help analyze relationships between customer desires, product design, and technical requirements. When done correctly, it reveals the best features to build to improve customer satisfaction.
The main benefit of QFD is that it ensures the customer is considered in both the design and development process, resulting in products that are more likely to satisfy your customers.
Key components of QFD
Before diving into the detailed process of quality function deployment, it is essential to understand its key components. These components form the foundation of the QFD methodology and help organizations effectively analyze and prioritize customer requirements.
In this section, we’ll discuss the house of quality, a core tool of QFD, and the voice of the customer (VOC), which lays the groundwork for gathering customer insights.
House of quality
Many people confuse the house of quality to be the same thing as QFD, but it’s actually the core tool of the QFD methodology. It contains several “rooms,” which create a house-shaped matrix:
There is no universally accepted version of the house of quality; you’ll see many slight variations, and it also changes as you go further along the methodology phases.
However, there are a few core rooms that frequently appear. Here’s a brief overview of each room:
- Left side — List of customer-requested features along with a weighted number for level of importance. This section is also known as “Hows”
- Right side — Competitive analysis with a weighted number of strengths or weaknesses of the customer-requested features
- Attic — Control factors, like product design or engineering. This section is also known as “Whats”
- Main room — Also known as the relationship matrix, the main room is a place to score the relationship between customer-requested features and control factors. A high relationship score means the control factor has a direct impact on satisfying the customer-requested feature. For example, if a control factor is the weight of a product, and customers request a lightweight product, then it has a high relationship score
- Roof — The roof covers the interrelationship section and describes the relationship between control factors
- Foundation — The importance rating is found here. The higher the number, the higher the priority it should be for development. The foundation calculated by evaluating the column of a control factor. For any column with a score in the relationship matrix, you multiply it by the corresponding weighted number of importance found on the left side to get the importance rating.
For example, a high relationship score is weighted at 9, and the customer-requested feature has a weighted importance of 3. Multiply 9 by 3, which equals 27, and that is the importance rating. Add this to any other relationship scores in the column, and you have the total importance rating.
Voice of the customer (VOC)
The first step of building the house of quality — and, subsequently, the entire QFD methodology — is to develop the voice of the customer (VOC). The VOC summarizes customers’ needs, wants, preferences, and desires associated with a product or service.
To develop the VOC, you need to create a solid market research report. Ideally, you should use a significant sample size to get the most accurate results.
There are a few ways to gather customer feedback to build the VOC, including:
Once you find specific items customers are requesting, then you can ask the customers how important it is to them to have that item, or you can rank items in order of importance. These items are then listed on the left side of the house of quality matrix, along with a weighted score of importance.
It’s crucial to develop the VOC correctly. Inaccurate information can skew the results of your market research and lead to poor deployment of the QFD.
What are the 4 phases of quality function deployment?
The four phases of quality function deployment are:
As mentioned earlier, you may find slight variations in the QFD methodology because there isn’t a universally accepted way to conduct the matrix. However, these four seem to comprise the closest thing there is to a standard model.
Many people tend to only focus on the first phase of the QFD method because this phase directly incorporates customer feedback and finds the relationship between this feedback and product specifications.
However, there are additional phases, and they have a waterfall effect on each other:
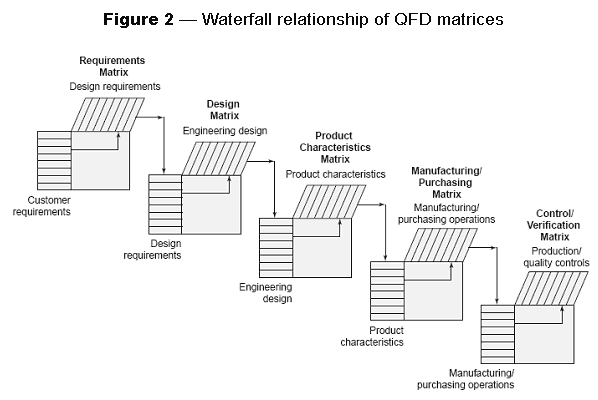
At the end of each phase, the control factors (listed on the top of each matrix) move to the left-hand side of a new matrix and a new set of control factors go on top. This helps identify additional opportunities or conflicts in areas such as design, product development, engineering, etc.
Let’s dive into the details of each phase.
1. Product planning
Th product planning phase begins with gathering customer feedback to develop the VOC. You’ll also identify the control factors. In this phase, it’s usually technical requirements. There may also be a competitive analysis to find the strength and weaknesses of your competitors.
Next, identify the relationship between the VOC and technical specifications to pinpoint what features to build next to satisfy customer needs. Ideally, this will be an area where your competitors are weak.
Product planning can help with the following goals:
- Prioritizing customer requirements
- Defining product requirements
- Creating a customer-focused product roadmap
2. Product development
Technical requirements move to the left side of the house of quality matrix, and a new set of control factors are put on top. The control factors for product development are usually critical parts or product specs.
In the product development phase, the goal is to recognize the key parts or specs to build a feature. It also helps with:
- Incorporating customer requirements into product design
- Collaborating with cross-functional teams
- Ensuring design consistency and quality
3. Process planning
Based on the product and component specifications found in the previous phase, this section identifies processes necessary to build features and deliver functionality. This is crucial information for production and quality teams.
Critical parts or product specs are on the left side of the house of quality matrix, and the control factors are steps to build the product specs. You should discover which process will have the best impact on creating the product specs.
This phase may be a good time for identifying verification and validation, including:
- Conducting prototype testing and customer trials
- Validating product design and functionality
- Gathering and analyzing customer feedback
4. Process quality control
This stage tends to be more crucial for manufacturing than software development. It’s designed to help you identify the best way to check the quality of the processes identified in the previous phase.
The house of quality matrix is built by putting processes on the right side, and the top section contains control specs. Then, your team can determine which controls are the most useful and create quality targets.
For SaaS companies, this phase can be part of the implementation and continuous improvement. For example:
What is an example of quality function deployment?
Here is a general example of how product teams can implement the QFD methodology:
- Develop the VOC by gathering customer feedback
- Once you’ve identified the features important to your customers, put them on the left side of the house of quality matrix and add a weighted score of the importance of each feature to this section
- Add the control factors to the top. In this product planning phase, it’s usually product specifications or design requirements.
- Competitor analysis is added to the right side of the phase, which is unique to this phase. It’s usually a weighted score of how competitors are doing compared to the VOC
- Identify the relationship between the VOC and the control factors by using the relationship matrix. You want to analyze what control factors can affect the VOC and assign a strong, medium, or low relationship score
- Review the interrelationships of the control factors and how they can impact each other
- Calculate the importance rating by multiplying the relationship score with the weighted importance factor in the VOC
- Analyze the results. A higher importance rating means that this may be the most efficient way of meeting your customers’ demands by building or improving certain features
- Further analyze your results by moving to the other three phases of the quality function deployment methodology
What is the role of QFD in product development?
Quality function deployment helps product development teams create customer-centric products. It takes every stage of the product development process and ensures the VOC is prioritized.
The house of quality matrix also promotes the discovery of features that complement each other. Along the way, it can help discover areas where your customer has an unmet need from you and your competitors.
Thanks to the structured method of the house of quality matrix, you can align the company’s potential with what the customer wants from your product suite.
While there are plenty of benefits to using QFD, there are a few drawbacks to consider:
- The house of quality matrix can get complex
- QFD may overindex on the customers’ opinions and negatively impact other areas of product development
- QFD can be costly because it takes time to gather customer feedback and process the data
- Some aspects of the house of quality matrix, such as determining the relationship matrix, are subjective. For the best results, ensure a multidisciplinary group reviews the matrix
Conclusion
Quality function deployment helps you keep the voice of the customer top of mind throughout the product development lifecycle. That way, customer needs and preferences are a driving force in creating a product suite that meets their expectations.
To put as fine a point on it as possible, quality function can help you validate whether you’re on the right path to satisfying your customers.
The post What is quality function deployment (QFD)? Phases, example appeared first on LogRocket Blog.
from LogRocket Blog https://ift.tt/tHF7VDh
Gain $200 in a week
via Read more
Source link
Leave a Reply